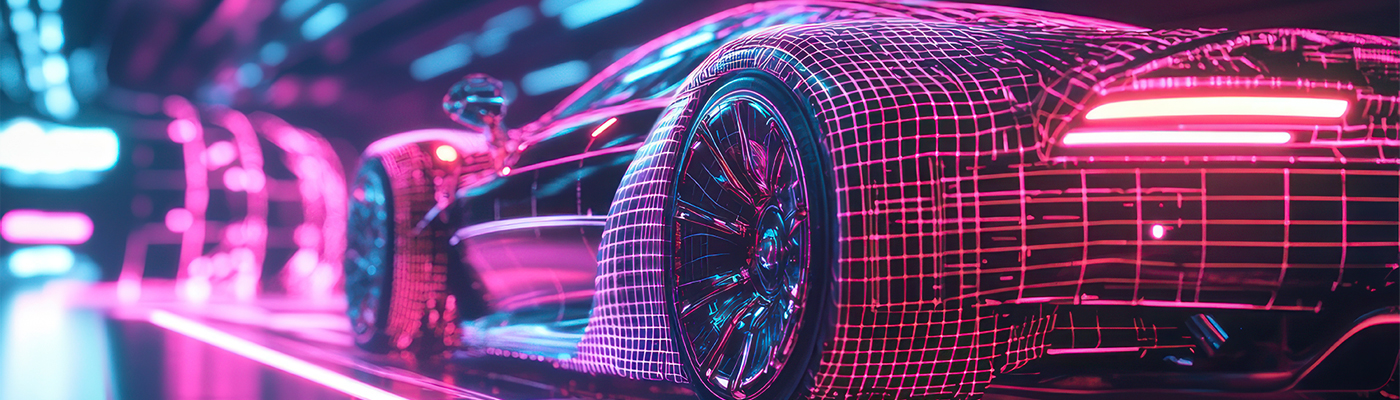
パワーデバイス(パワー半導体)製造装置Power Device Solution
パワーデバイス製造装置に関するお問い合わせ車社会を取り巻く環境が変化しました。カーボンニュートラルや安全対策、自動運転対応を見据えた技術的対応が強く求められ、世界各国では、plug-in hybrid electric vehicle(PHEV)、electric vehicle(EV)、full cell vehicle(FCV)等の開発が進められています。
その中で重要な役割を果たすのが、power control unit(PCU)などの半導体デバイスであり、これらのデバイスは高電圧・大電流を制御するために不可欠です。
PCUには、インバータやコンバータ、周波数変換機能をもつ電力交換器が含まれ、これを構成するキーデバイスがパワー半導体、すなわちパワーデバイスと呼びます。
今後ますます必要となる効率的なエネルギー変換と制御を実現するために、アルバックは様々な開発のもとソリューションを提案しています。
INDEX
トレンチ構造パワーデバイスの製造工程における課題とソリューション
① イオン注入(N+注入)
② イオン注入( AI+注入)
③ トレンチ加工用マスク成膜
④ マスクエッチング⑤ トレンチエッチング
⑥ カーボンキャップ成膜
⑦ 活性化アニール&カーボン除去
⑧ ゲート電極形成
⑨ ゲート絶縁膜形成
⑩ ソース電極形成⑪ 裏面電極形成
- ① SiC製造工程におけるイオン注入の課題
-
高・低濃度注入の使い分け
SiCは高濃度注入を行うと結晶欠陥が発生し、アニールで回復しないので高温での処理が必要になります。一方、低濃度の注入では常温注入の方が特性が良いことが知られています。- ⑤ SiC製造工程におけるトレンチ形成の課題
ゲートトレンチ形状
高耐圧用途では電界集中を避けるため、トレンチ構造底部にラウンド形状が必要です。また、SiCは固く、化学的に安定した材料のため高エッチングレートの実現が困難です。- ⑥ SiC製造工程におけるカーボンキャップ形成の課題
SiC表面荒れ
キャップレスでアニールを行うとSi抜けが発生し、表面粗さが顕著になります。- ⑪ SiC製造工程における裏面電極形成の課題
基板反りによる歩留り低下
反ったウェハをミスなくハンドリングする技術と薄ウェハの割れや反りを回避するための高度な応力コントロール技術が重要になります。
パワーデバイス製造工程におけるULVAC装置によるソリューション
- 課題高濃度・低濃度注入の両立
高・低濃度注入の使い分け
SiCは高濃度注入を行うと結晶欠陥が発生し、アニールで回復しないので高温での処理が必要になります。一方、低濃度の注入では常温注入の方が特性が良いことが知られています。
- 解決高温と常温注入を瞬時に切り替え
-
高温と常温注入を瞬時に切り替えられるデュアルプラテンを搭載し、高スループットが可能になりました。
また、高温処理はアルバック独自の基板の昇温方式により高温でのプロセス安定性、搬送信頼性を実現します。DOSE
2E20/㎤Implantation Temperature 高温(500℃) Room Temp. RHEED Pattern after Anneal Poly-type 4H-SiC 3C-SiC 高濃度注入の場合
トレンチ形成のソリューション
- 課題ゲートトレンチ形状
高耐圧用途では電界集中を避けるため、トレンチ構造底部にラウンド形状が必要です。また、SiCは固く、化学的に安定した材料のため高エッチングレートの実現が困難です。
- 解決スムーズな側壁とラウンド形状の実現
-
側壁の平滑性と高い選択比を両方実現するプロセスによりエッチング条件を最適化して、スムーズな側壁とラウンド形状を実現します。 SiO2マスクに対する高い選択比を維持しつつ、対SiCで、700nm/min以上のエッチングレートを実現します。
material SiC mask SiO2 size Wide1um,Depth2.1um Etching Rate 700nm/min Selectivity >8.0
カーボンキャップ成膜のソリューション
- 課題SiC表面荒れ
-
キャップレスでアニールを行うとSi抜けが発生し、表面粗さが顕著になり、1900℃のアニール後ではRaが13.3nmまで増加し、ステップバンチングが発生(①)。
一方レジストでカーボンキャップを行うと同条件でRaが0.78nmに低減(②)しますが更なる最適化をおこなう必要があります。① Cap-less
Ra 13.3nm② Resist Carbon-cap
Ra 0.78nm
- 解決緻密なC被膜形成
-
アルバックのスパッタによるカーボンキャップは緻密で、Siの抜けを効率的に抑制し、AFM観察でも平滑な表面形成が確認できます。 1900℃アニール後でRaが0.16nmまで低減(③)します。
③ Sputter Carbon-cap
Ra 0.16nm
裏面電極形成のソリューション
- 課題基板反りによる歩留り低下
反ったウェハをミスなくハンドリングする技術と薄ウェハの割れや反りを回避するための高度な応力コントロール技術が重要になります。
- 解決ESCステージを用いた応力制御
反り基板対応の搬送技術、応力制御技術の確立
例えば特殊冷却ステージを使用し温度制御するという方法があり、応力を軽減させることができます。アルバックの技術により、下のグラフの通り、スパッタ圧力を変え応力ゼロを出現させることができ、反りのない基板搬送も可能です。
特に高価なSiC基板に対しては効果がクローズアップされます。ULVAC Special process アルバック独自の特殊ウェハステージにより、反りと歪みを最低限に抑えることができます。
STD Condition Niのストレスが高い為、反りが発生します。
パワーデバイス(パワー半導体)製造 関連装置